- Information for Middle and High School Researchers
Strong, environmentally friendly plastic
2020.10.08
Strong, environmentally friendly plastic
Dr. Tatsuo Kaneko, Professor of Environment and Energy, School of Advanced Science and Technology, Japan Advanced Institute of Science and Technology
While it is important to prevent waste from spilling into the environment, it would be better if the spilled waste would disappear naturally... In Japan, the use of biodegradable plastics for disposable tableware at the 2005 World Exposition in Aichi attracted much attention, but they are still not fully utilized. Dr. Kaneko of the Japan Advanced Institute of Science and Technology (JAIST) aims to solve this problem by developing highly functional and highly degradable plastics.
Challenges of polylactic acid, a representative biodegradable plastic
When it comes to biodegradable plastics, polylactic acid, which is made from corn and other materials, is a well-known material. It was actually used at the Aichi Expo, but its degradability has its own problems. Normally, polylactic acid is very stable when its molecular weight is in the tens of thousands to hundreds of thousands, and it is not degraded by microorganisms until its molecular weight is reduced to about 10,000 through hydrolysis in a hot and humid environment. Therefore, in fact, when it leaks into the marine environment and other areas, it becomes a stable waste just like conventional plastics.
One of the difficulties in considering this issue is that the material must have seemingly contradictory properties: it must have sufficient heat resistance and strength, yet be easily degraded. In addition, low production costs are also important for widespread use in society. Kaneko is developing a new plastic material that meets these requirements based on itaconic acid, a raw material produced through fermentation by mold.
Made from mold, heat and force resistant
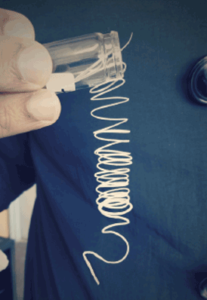
Fig. 1 Nylon fiber derived from itaconic acid
Itaconic acid is a natural molecule produced from sugar by filamentous fungi through fermentation. It is already produced industrially as a starting material for food additives and some chemical products. Kaneko has developed a method for synthesizing bionylon, a polymer made from itaconic acid and diamine (Figure 1). This bionylon has a glass transition temperature of 154°C, which is the temperature at which it becomes more fluid when heated further, and can withstand much higher temperatures than polylactic acid, which is around 60°C, or nylon 6 or nylon 6,6 used in clothing. Because of its low glass transition temperature, polylactic acid requires the addition of another material as an additive when used in dishes for serving hot food, for example. By contrast, this bionylon is extremely heat-resistant on its own.
Not only that, it also shows high performance comparable in strength to polycarbonate resin, which is used for various applications including the bodies of electrical appliances and suitcases. Despite its weakness in tensile strength (not high elongation at break), other mechanical properties are high, making it a promising material.
Nearly decompose under natural conditions
Itaconic acid-derived bionylon also shows excellent degradability. For example, when irradiated with UV-A and UV-B contained in sunlight using a mercury vapor lamp, it has been found to degrade in 6 hours (Figure 2). In addition, after one year of reclamation in alkaline (pH 7.5-7.9) soil at a depth of 2-4 cm, 841 TP3T remained in polylactic acid, while bionylon almost disappeared (Figure 3).
This property could be used, for example, in mulch used in fields to control weed generation and soil runoff, eliminating the need for farmers to remove the mulch and improving their work efficiency. It could also be used as a material for indoor toys. Mr. Kaneko also has an idea to add this material to other plastics to make them more degradable, and future research should lead to even more applications.
Figure 3 Soil degradability of various bionylons and polylactic acid
(The leftmost one is polylactic acid; the second and subsequent ones are bionylon synthesized from (1) ethylenediamine, (2) propylenediamine, (3) butylenediamine, and (4) pentamethylenediamine).
Can we expand the use of bio-based plastics in society?
Most plastic products produced and used to date are made from petroleum. The origin of these products can be traced back hundreds of millions of years ago, when organisms synthesized organic substances from the energy of sunlight and CO2 to create their bodies, and the carcasses of these organisms were transformed over a long period of time. In other words, our lives are supported by the raw materials of CO2 in the atmosphere hundreds of millions of years ago. The development of itaconic acid-derived nylon and other biomass plastics is an effort to replace this raw material with CO2 in the atmosphere of today.
Nevertheless, replacing materials that are the backbone of various product manufacturing is not an easy task. In addition to performance, it is also necessary to consider production volume and cost, as well as the establishment of a stable supply system. In fact, Kaneko estimates that the production cost of itaconic acid-derived nylon is slightly higher than that of conventional nylon 6,6 (nylon 66: 860 yen/kg, itaconic acid-derived nylon: 970 yen/kg). In order to reduce waste, curb climate change, and restore a livable planet for non-human creatures, can we pick up products that are better for the environment, even if they cost a little more? The choices each of us makes will be the key to creating the future.
*Reprinted from "Education Support vol. 47